Two methods. Endless advantages
Stop digging! With Inpipe technology you can reline up to 300 meters of pipes in one day without excavation. This is how it is done.
The solution
A soft and malleable fiberglass-reinforced polyester liner is inserted into the pipe. The liner is inflated with compressed air and cured in place with UV light, creating a new pipe inside the old one. The ends are cut and service connections are opened. In one day, you can have up to 300 meters of pipe renovated. Curing with UV light is energy-efficient in comparison with, for example, curing with steam or hot water and no process water has to be disposed of. You save up to 80 percent of the cost and reduce CO2 emissions by up to 80 percent compared to digging.
Inversion
The liner is manufactured inside out and becomes inverted when it is being pushed into the pipe using compressed air. This requires minimal human resources compared to other methods and improves safety by minimizing the need to work in wells, since the majority of the operation takes place inside an installation vehicle.
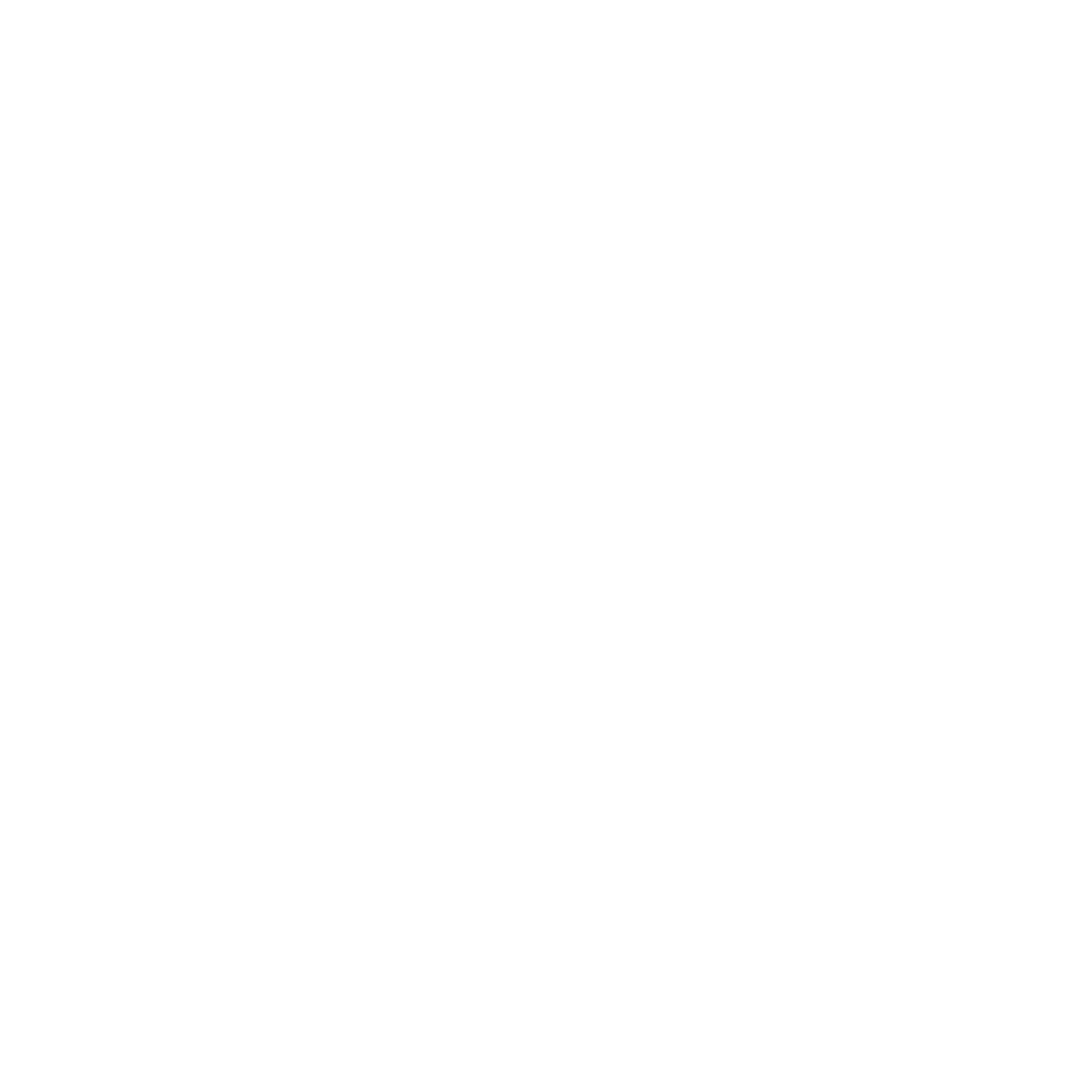
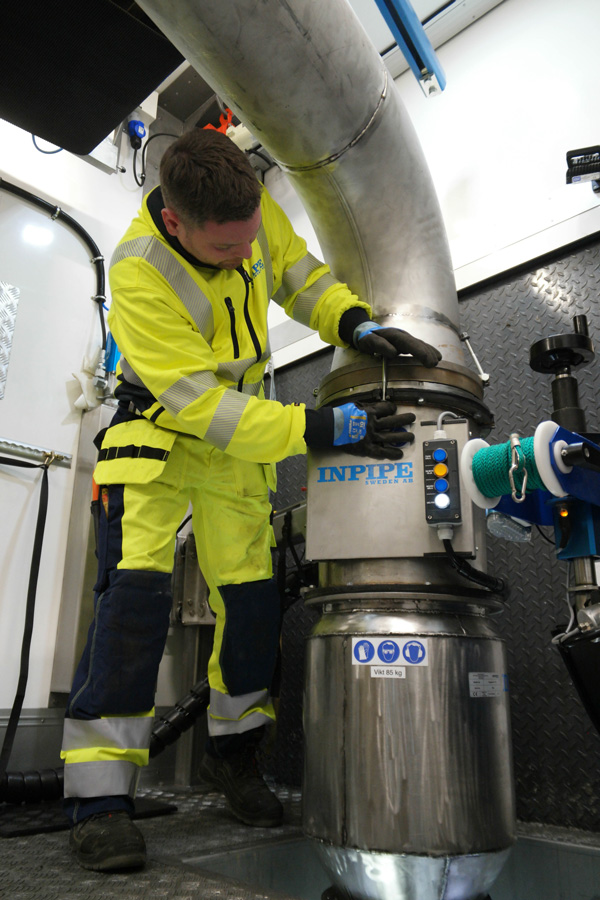
Advantages of inversion
- Fast installation, resource-efficient and environmentally friendly.
- Provides minimal gap between the existing pipe and the liner.
- Safe working environment, minimizing work in a well.
- Retains the shape and flow on your wires.
- Adapted for a liner up to and including
Ø500 mm - Requires fewer work steps than winch-in-place
- You do not need a tow line in the pipe to be able to pull out wires or ropes
- It requires fewer staff resources.
WIP –
Winch-In Place
The WIP method is pulling the liner into place using a rope or wire. Inpipe has further developed other WIP methods to inflate the liner and insert the UV light train directly from the installation vehicle. The installer does not have to expose him or herself to dangers by handling the UV light train in a narrow well.
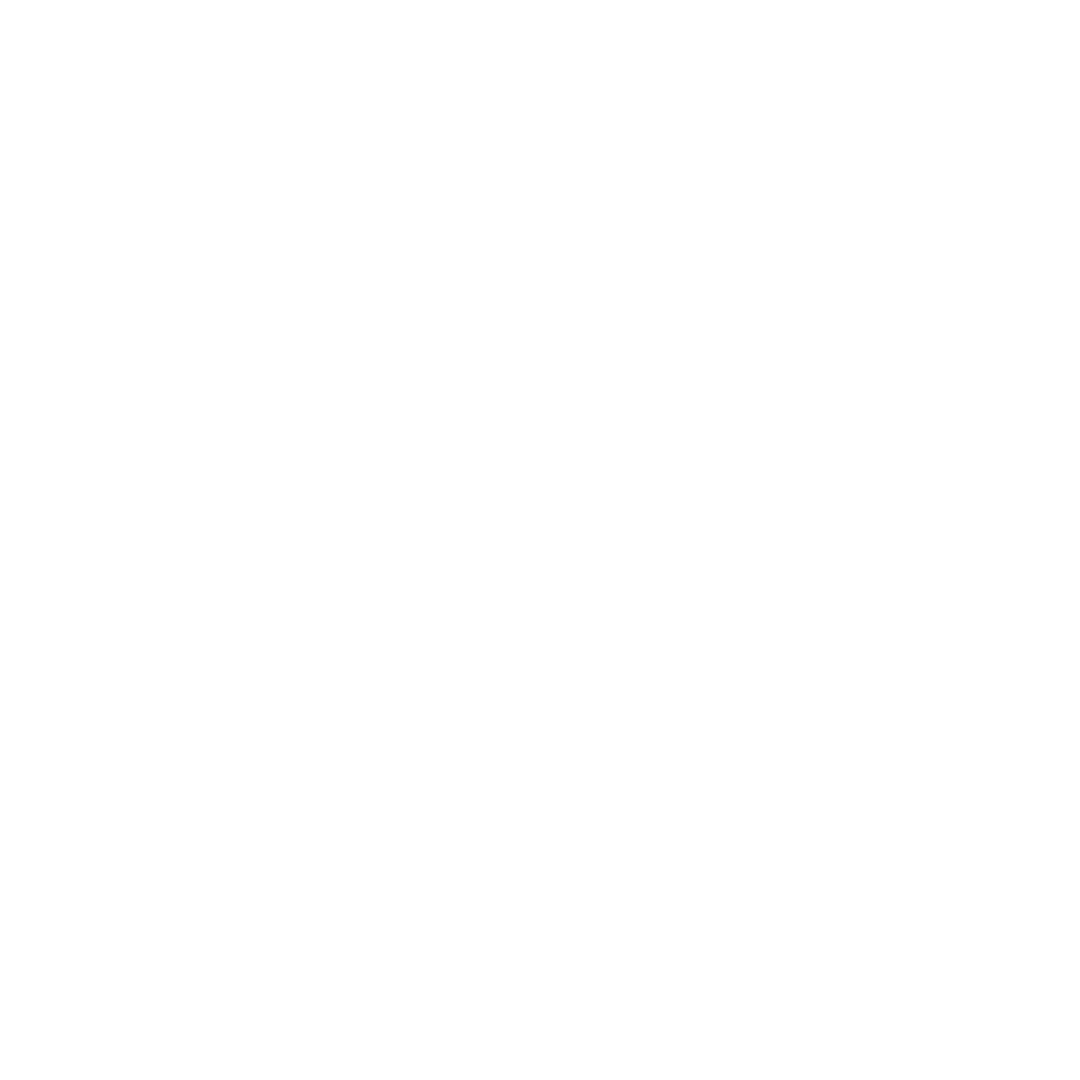
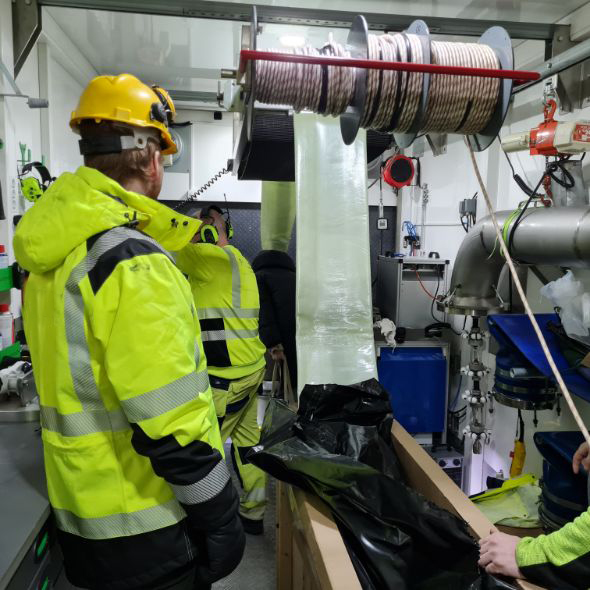
Advantages of WIP
- Environmentally friendly
- Cost effective
- Safe working conditions
- Minimal disturbance to the surroundings and traffic
- Tight fit between the liner and the existing pipe
UV light curing
When UV light hits polyester with photo initiators, a chemical reaction takes place that causes the polyester to harden. This is a fast and energy-efficient process in comparison with heat-cured liners. It is also a safer method, since it is not affected by ambient temperatures. Curing with UV light has a smaller climate footprint and you avoid handling process water that may contain chemicals, such as styrene.
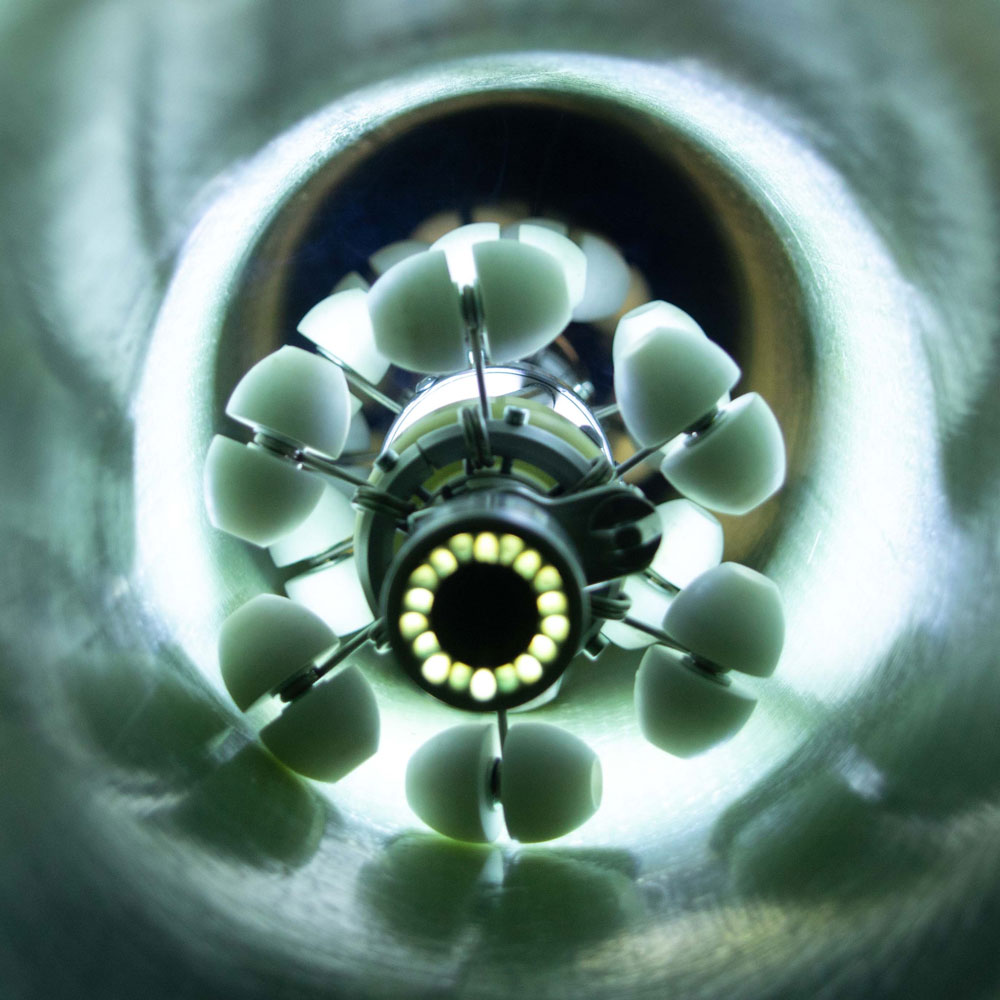
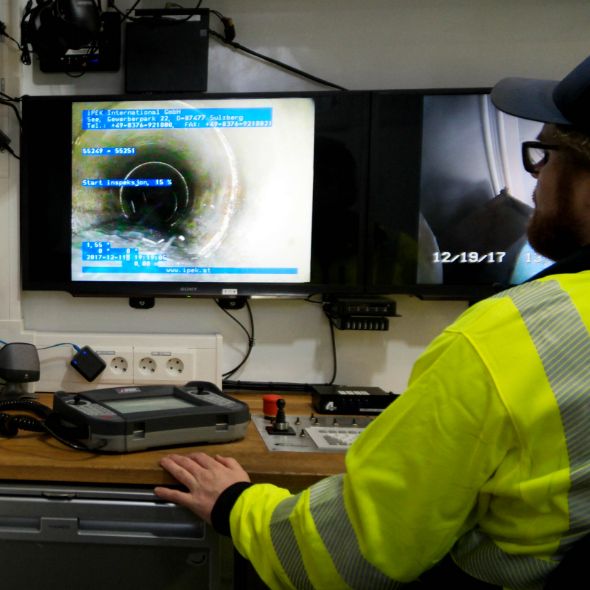
Advantages of UV curing
- The method can harden up to 90 meters of liner per hour depending on dimension and thickness
- Low energy consumption keep emissions to a minimum
- No process water is formed that can contain harmful chemicals
- The equipment takes up little space
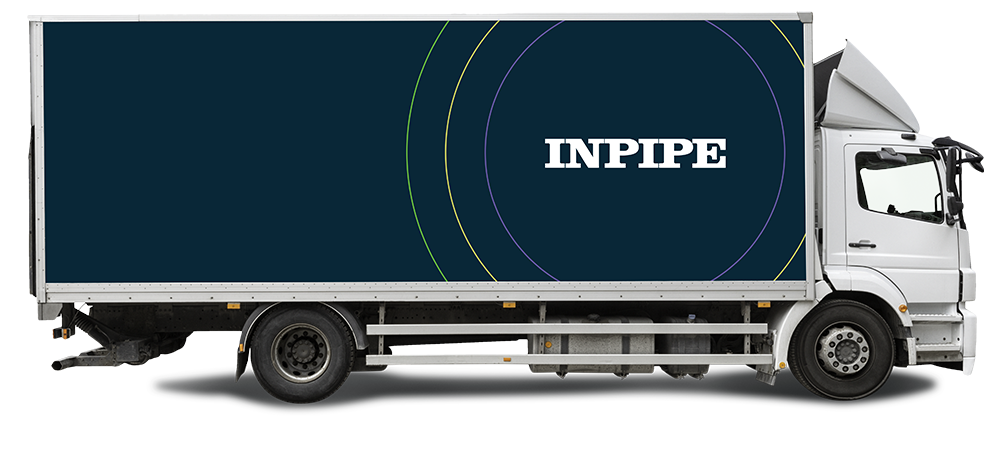
Inpipe lining system
Complete installation equipment
Inpipe offer products for two ways of installation – Inversion and Winch In Place.